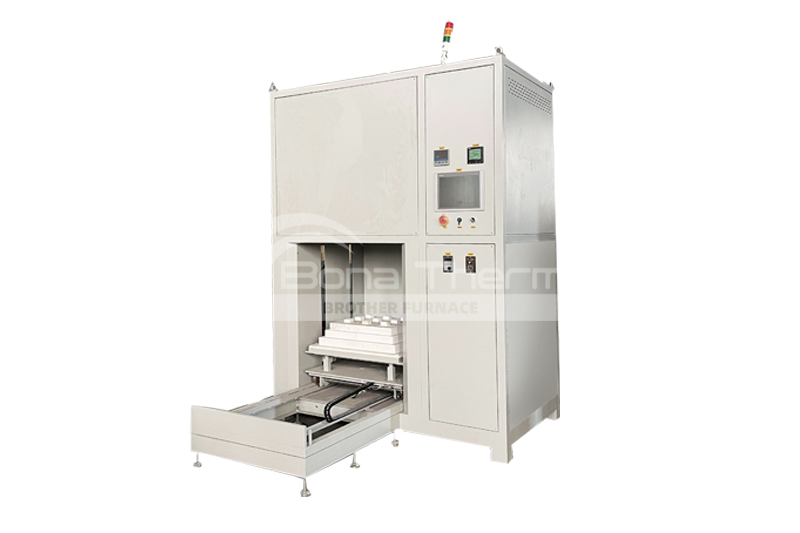
- Integrated Debinding and Sintering Design
- Provide ChamberCustomization Service
- Max. Temp. 1700℃
- Intelligent Temperature Control System (Supports multi-stage programming)
- Inert Gas Protection (Prevents oxidation)
- Real-Time Monitoring and Alarm System
Leave message now!
Lifting Furnace Structure Display
-
The chamber of lifting furnace
-
The side of lifting furnace
-
The lifting platform of lifting furnace
-
The back of the lifting furnace
-
Furnace Lining Material
The oxidation furnace uses a polycrystalline limit refractory lining, with a mullite-based furnace bottom that provides excellent load-bearing capacity.
-
Lifting System
Principle: The motor drives the screw to rotate, and the nut moves along the axis of the screw achieve lifting.
Structure: Servo motor + precision screw + guide mechanism (linear guide rails).
-
Temperature Control System
Siemens PLC, 10-inch temperature control screen, and Yudian temperature controller.
Temperature control accuracy can reach ±1°C.
Up to 50-stage automated heating and cooling programs can be set.
-
Feeding System
Fully automated feeding and unloading trolley, equipped with limit and safety devices.
-
Gas Inlet System
The temperature of the gas entering the furnace is controlled according to the requirements of different stages, along with the gas flow.
The preheated gas inlet system can achieve rapid cooling inside the furnace.
Inert gases such as nitrogen and argon can be introduced based on customer requirements.
Model | Max Temp(℃) | Work Temp(℃) | Chamber Size(W*H*D)mm | Volume(L) | Power(kW) | Phase | Heating Element | Thermocouple |
---|---|---|---|---|---|---|---|---|
BR-17BL-8 | 1700 | 1600 | 200*200*200 | 8 | 6 | 1 | MoSi2 | B type |
BR-17BL-12 | 1700 | 1600 | 200*200*300 | 12 | 8 | 1 | MoSi2 | B type |
BR-17BL-27 | 1700 | 1600 | 300*300*300 | 27 | 12 | 3 | MoSi2 | B type |
BR-17BL-36 | 1700 | 1600 | 300*300*400 | 36 | 15 | 3 | MoSi2 | B type |
BR-17BL-64 | 1700 | 1600 | 400*400*400 | 64 | 20 | 3 | MoSi2 | B type |
Model | Max Temp (℃) | Work Temp (℃) | Chamber Size (W*H*D)mm | Volume (L) | Power (kW) | Phase | Heating Element | Thermocouple |
---|---|---|---|---|---|---|---|---|
BR-17HBL-8 | 1750 | 1650 | 200*200*200 | 8 | 6 | 1 | MoSi2 | B type |
BR-17HBL-12 | 1750 | 1650 | 200*200*300 | 12 | 8 | 1 | MoSi2 | B type |
BR-17HBL-27 | 1750 | 1650 | 300*300*300 | 27 | 12 | 3 | MoSi2 | B type |
BR-17HBL-36 | 1750 | 1650 | 300*300*400 | 36 | 15 | 3 | MoSi2 | B type |
BR-17HBL-64 | 1750 | 1650 | 400*400*400 | 64 | 20 | 3 | MoSi2 | B type |
Other Furnace Types
Brother Furnace provides a wide range of debinding and sintering furnaces, having developed various new furnace models that significantly improve the efficiency and effectiveness of the debinding and sintering processes. Through continuous innovation, Brother Furnace provides efficient and energy-saving solutions to meet the needs of different materials and processes across industries.
The main types are as follows:
-
Debinding and Pre-Sintering Integrated Furnace
View Products+
-
Lifting Debinding Sintering Furnace
View Products+
-
Lifting Atmosphere Sintering Furnace
View Products+
-
Hydrogen Debinding Sintering Furnace
View Products+
-
Hot-Air Circulation Debinding Furnace
View Products+
Leave message now!
What Are the Advantages of Brother Furnace’s Lifting Furnace?
-
Strong R&D Capability
The one-piece design integrates the electrical control system at the bottom, featuring a double-layer shell with air circulation insulation for enhanced safety and energy efficiency.
-
High-Purity Alumina Furnace Chamber
Made from lightweight, high-purity alumina, ensuring high hardness, no powder shedding, and no volatile emissions at high temperatures, meeting international industry standards.
-
Superior Heating Elements
Utilizes high-quality U-shaped hot-bent molybdenum disilicide (MoSi₂) rods for dual-side heating, ensuring excellent temperature uniformity.
-
Fully Automatic Operation
Once the program is set, the furnace automatically completes the entire heating and cooling process, eliminating the need for manual monitoring.
-
Over-Temperature Protection
Equipped with an alarm and automatic protection mechanism to ensure operational safety.
-
Intuitive Control Panel
Features power and heating indicator lights for real-time monitoring of equipment status.
Application Scenarios
Ceramic Materials
Lifting furnaces are widely used in the ceramic industry for high-temperature sintering, annealing, and heat treatment. Depending on the characteristics and applications of various ceramic materials, their usage scenarios can be categorized as follows:
1. Sintering of Precision Structural Ceramics
Precision structural ceramics, known for their high-temperature resistance, corrosion resistance, and superior mechanical strength, are extensively used in aerospace, automotive manufacturing, and medical devices. Lifting furnaces provide a uniform and stable high-temperature environment to ensure ceramic densification and enhanced mechanical properties. Common applications include:
- Zirconia ceramics (ZrO):Dental implants, cutting tools, wear-resistant components.
- Alumina ceramics (AlO):Electronic packaging, refractory materials.
- Silicon carbide ceramics (SiC): High-temperature furnace linings, semiconductor equipment components.
- Silicon nitride ceramics(SiN):Bearings, automotive engine components.
2. Sintering of Electronic Ceramics
Electronic ceramics are essential components in electronic devices. Lifting furnaces are used for precise sintering and annealing to ensure stable dielectric, conductive, or piezoelectric properties. Common applications include:
- Multilayer ceramic capacitors (MLCCs):Core components in electronic devices.
- Piezoelectric ceramics (PZT, BaTiO₃):Sensors, ultrasonic devices.
- Dielectric ceramics:Microwave communication, wireless charging.
- Semiconductor ceramics:Thermistors, gas sensors.
3.Sintering of Functional and High-Temperature Ceramics
Functional ceramics possess unique physical and chemical properties and are widely used in new energy, optoelectronics, and environmental applications. Lifting furnaces ensure precise temperature control and atmosphere regulation for maintaining the functionality and stability of these materials. Typical applications include:
- Solid oxide fuel cells (SOFCs):Energy conversion systems.
- Transparent ceramics (YAG, MgAl₂O₄):High-power lasers, infrared windows.
- High-temperature superconducting ceramics (YBCO, BSCCO):Magnetic levitation, superconducting cables.
4.Sintering of Ceramic Matrix Composites
Ceramic matrix composites (CMCs) offer enhanced strength and heat resistance, making them essential in aerospace and defense applications. Lifting furnaces are used for sintering the following materials:
- C/SiC silicon carbide composite ceramics:Aerospace brake pads, spacecraft thermal protection systems.
- SiC/SiC ceramic matrix composites:Gas turbine blades, high-temperature turbine components.
- AlO/TiC composite ceramics:Wear-resistant coatings, cutting tool materials.
5.Heat Treatment of Glass Ceramics and Ceramic Coatings
Glass ceramics and ceramic coatings require precise thermal treatment to enhance their optical, thermal, and mechanical properties. Lifting furnaces are suitable for:
- Glass-ceramics:High-temperature furnace linings, optical components.
- Transparent ceramics (e.g., laser crystal YAG):Laser equipment, optical lenses.
- Ceramic coatings (zirconia, alumina):Gas turbine blade protection, high-temperature aerospace coatings.
-
Heat treatment for 3Dprinted metal parts
-
Precision structural ceramics
-
SiC silicon carbide ceramics
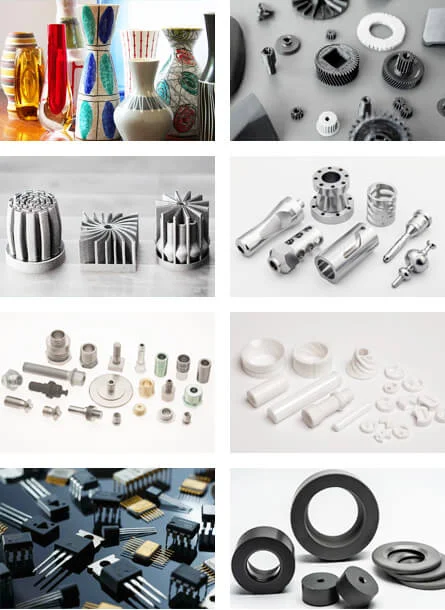
-
Semiconductor and Optoelectronic Materials
Sintering and heat treatment of semiconductor materials such as silicon carbide (SiC) and gallium nitride (GaN)
High-temperature annealing of optoelectronic materials such as LEDs and solar cells
-
Metal Heat Treatment
Annealing and sintering of high-temperature alloys and refractory metals
High-temperature treatment of precision metal components, including heat treatment for 3D-printed metal parts
-
Glass and Advanced Functional Materials
Sintering and annealing of glass ceramics
Preparation of high-temperature superconducting materials
Debinding and Sintering Process
-
Powder preparation
>>
-
Granulation
>>
-
Molding process
>>
-
Debinding
>>
-
Sintering
>>
-
Debinding Stage
The debinding process typically employs thermal debinding, where the organic binder undergoes melting, decomposition, and volatilization through heating, ultimately being removed from the ceramic body. The key to thermal debinding lies in controlling the heating rate, atmosphere, and pressure to ensure complete removal of organic components while preventing cracks or deformation.
PS:The principle of thermal debinding
Thermal debinding involves heating the green body to cause the organic binders to undergo melting, decomposition, and volatilization, ultimately removing them from the material. The key to thermal debinding lies in controlling the heating rate, atmosphere, and pressure to ensure the complete removal of organic components while preventing cracking or deformation of the green body.
-
Sintering Process
The sintering process is a critical step in ceramic material preparation, where ceramic powder particles are consolidated into a dense solid material through high-temperature treatment. During sintering, particles undergo diffusion, grain growth, and pore elimination, resulting in ceramics with high strength, high density, and excellent performance.
Ps:The main sintering methods include pressureless sintering, hot pressing, hot isostatic pressing (HIP), and atmosphere sintering.
The lifting debinding and sintering furnace is designed to achieve stringent debinding and sintering processes.
Industry Solutions
Brother Furnace has provided professional lifting debinding sintering furnace's cases for customers in many industries.
Industry | Typical Process | Customer Case | Key Control |
---|---|---|---|
Electronic Ceramics |
MLCC sintering, AlN substrate preparation |
Fenghua Advanced Technology (MLCC consistency improved by 30%) |
Heating rate ≤5°C/min (to prevent cracking) |
Metal Powder Metallurgy |
Ti-6Al-4V sintering, WC-Co hard alloy |
Aerospace fastener manufacturer (density ≥98%) |
Rapid argon cooling at 200°C/min (α+β dual-phase structure) |
New Energy Batteries |
LiFePO₄ carbon coating, Si-C anode sintering |
CATL (cell cycle life improved by 20%) |
Ar gas quenching to suppress Fe³⁺ reduction |
Special Ceramics |
SiC reaction sintering, Y-TZP stabilization |
Jingdezhen Jingda (yield rate ≥95%) |
Nitrogen atmosphere + rapid cooling to retain tetragonal phase |